In a fast-paced and competitive business world, maintaining excellence is more critical than ever. Quality assurance (QA) plays a vital role in upholding high standards and ensuring the delivery of top-notch products or services. From startups to global corporations, businesses recognize the significance of implementing effective QA processes to meet customer expectations and thrive in a dynamic marketplace.
What is Quality Assurance?
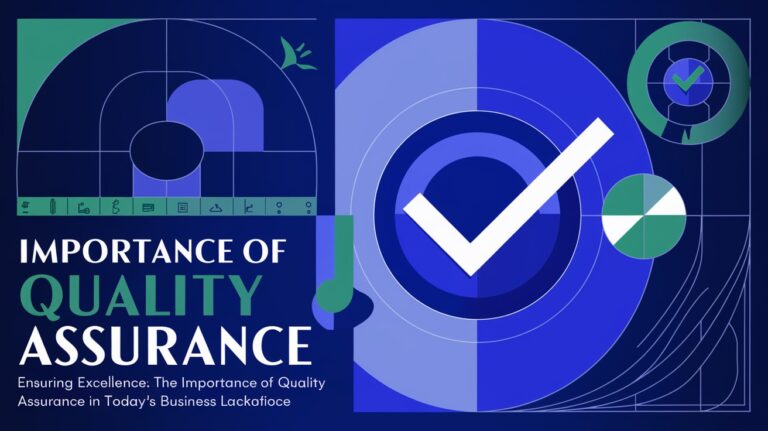
Quality assurance (QA) refers to the systematic processes and methodologies used by organizations to ensure that their products or services meet predefined quality standards. It focuses on building quality into the production process from the beginning rather than merely inspecting the final output. By adopting a proactive approach, QA emphasizes preventing defects, fostering continuous improvement, and aligning outcomes with customer expectations and regulatory requirements.
Key characteristics of QA include:
Establishing clear standards and guidelines.
Monitoring and improving processes to maintain consistency.
Ensuring compliance with industry standards and customer needs.
Why is Quality Assurance Important?
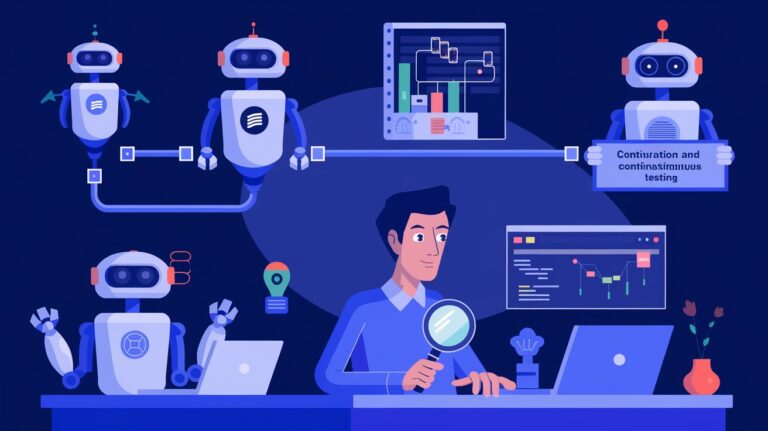
Quality assurance is more than a functional necessity; it’s a strategic asset for businesses. Here’s why it matters:
Enhanced Customer Satisfaction:
QA ensures that products and services consistently meet or exceed customer expectations.
By reducing defects and errors, businesses foster trust and loyalty among their customers.
Cost Efficiency:
Addressing issues during production is more cost-effective than fixing them post-launch.
Effective QA processes reduce expenses related to product recalls, warranty claims, and customer complaints.
Competitive Advantage:
Delivering superior quality helps businesses differentiate themselves in a crowded market.
QA-driven innovation enhances product reliability and brand reputation.
Regulatory Compliance:
Adhering to industry standards minimizes legal risks and ensures market access.
Quality Assurance vs. Quality Control
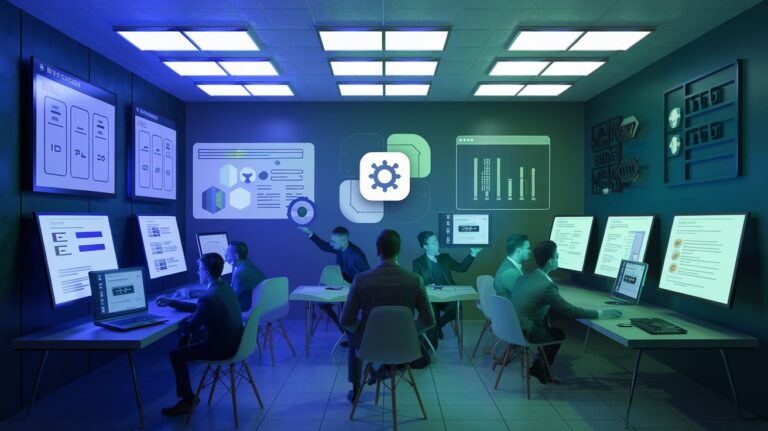
While often used interchangeably, quality assurance and quality control serve different purposes:
Quality Assurance (QA):
Focuses on preventing defects.
Involves process-oriented activities like establishing standards and improving workflows.
Quality Control (QC):
Focuses on identifying defects.
Involves product-oriented activities like testing and inspection.
Both QA and QC are integral to achieving comprehensive quality management.
Steps to Implement an Effective QA Program
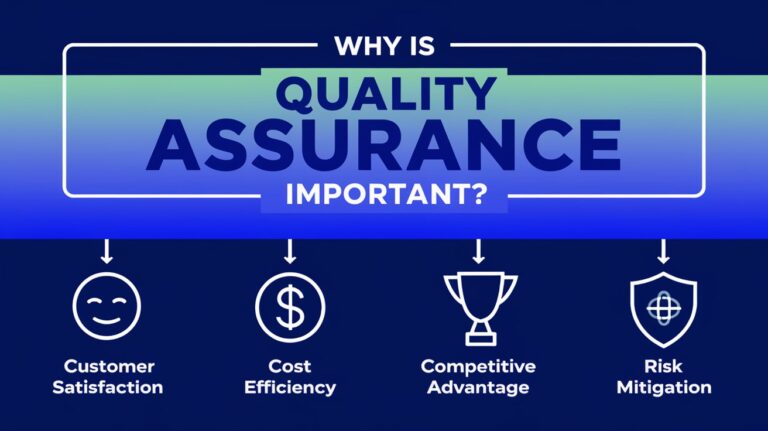
Define Quality Objectives:
Align QA goals with organizational objectives and customer expectations.
Identify key performance indicators (KPIs) to measure success.
Develop a QA Plan:
Outline processes, resources, and responsibilities.
Ensure cross-department collaboration for comprehensive QA coverage.
Train Teams:
Provide employees with the knowledge and tools needed to follow QA processes effectively.
Monitor and Audit:
Conduct regular audits to assess compliance and identify areas for improvement.
Use data-driven insights to refine processes.
Foster Continuous Improvement:
Encourage feedback loops to adapt QA practices to evolving customer needs and market trends.
Benefits of Quality Assurance
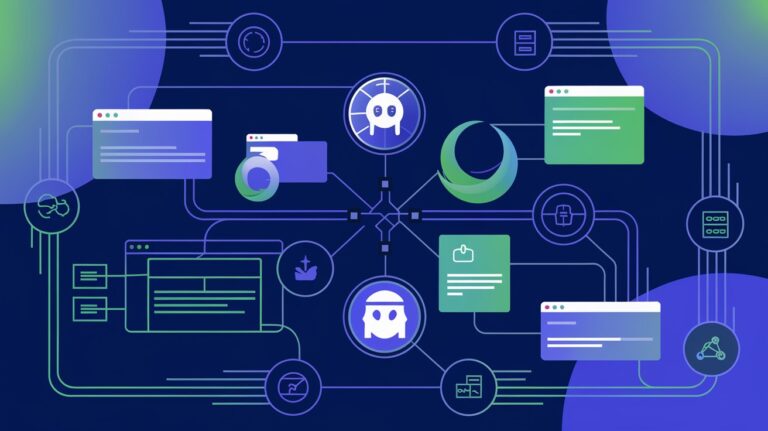
Implementing a robust QA program offers numerous advantages:
Improved Operational Efficiency:
Streamlined processes minimize waste and optimize resource allocation.
Risk Mitigation:
Early detection of potential issues reduces the likelihood of costly recalls or legal disputes.
Enhanced Brand Reputation:
Consistently delivering high-quality products builds customer trust and loyalty.
Increased Profitability:
Efficient QA practices lead to better resource utilization and higher customer retention rates.
Tools and Technologies for Quality Assurance

Modern QA practices leverage advanced tools and technologies to enhance efficiency and accuracy:
Automated Testing Tools:
Examples: Selenium, TestComplete, JMeter.
Automate repetitive testing tasks to save time and reduce errors.
Project Management Software:
Data Analytics Tools:
Examples: Tableau, Power BI.
Analyze quality metrics and identify areas for improvement.
Artificial Intelligence and Machine Learning:
Predict and address potential quality issues before they occur.
QA Across Industries
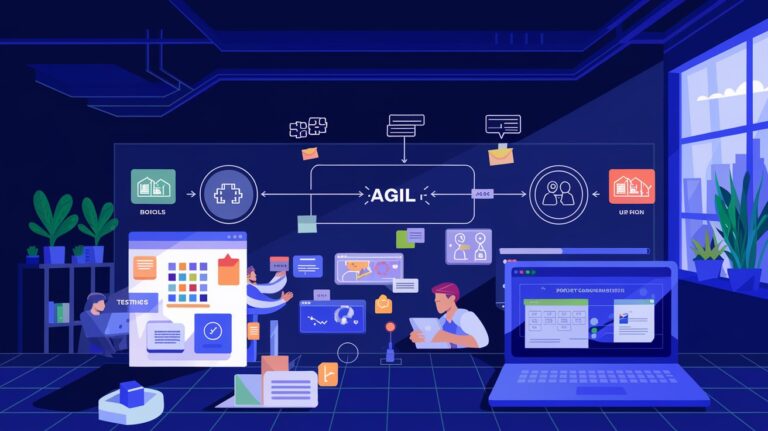
Quality assurance is crucial in various sectors, each with unique requirements:
Manufacturing:
Ensures products meet safety standards and regulatory compliance.
Techniques like Six Sigma and TQM optimize production processes.
Software Development:
Focuses on testing applications for functionality, performance, and security.
Agile and DevOps methodologies integrate QA throughout the development lifecycle.
Healthcare:
Emphasizes patient safety and compliance with strict industry regulations.
Conclusion: The Future of Quality Assurance
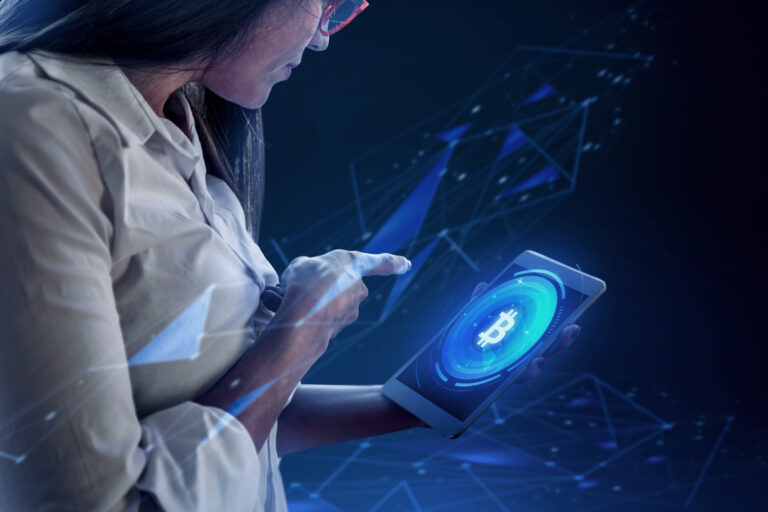
As customer expectations and technological advancements continue to evolve, quality assurance will remain a cornerstone of business success. By integrating advanced tools, fostering a culture of continuous improvement, and prioritizing quality at every stage, organizations can meet market demands and secure a competitive edge.
Investing in QA is not just about meeting standards—it’s about exceeding them. By doing so, businesses can deliver exceptional value to their customers and achieve sustainable growth in an ever-changing landscape.